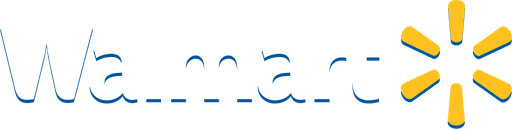
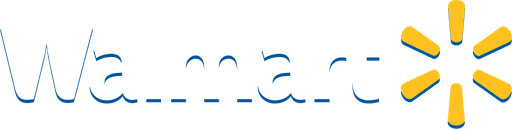
Sr. UX designer - Propriety enterprise apps
Sr. UX designer - Propriety enterprise apps
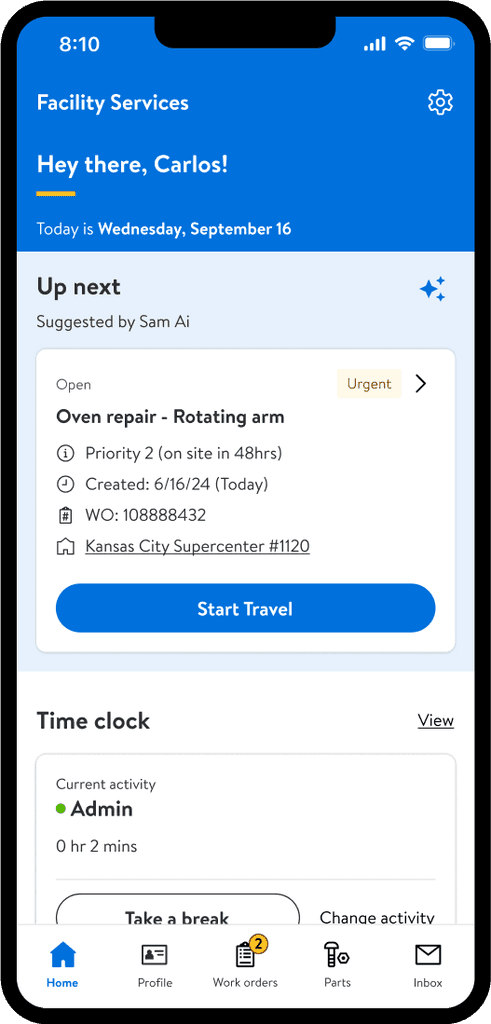
CASE STUDY
CASE STUDY
CASE STUDY
Walmart technician experience app
Walmart technician experience app
Walmart technician experience app
I led the process to create a new app for Walmart technicians to replace the outdated legacy system. Leveraged AI to prioritize work orders, simplify workflows, and reduce the reliance on multiple tools—ultimately boosting efficiency and reducing technician turnover.
Role
Sr. UX designer
Domain
Propriety enterprise apps
Consulted
Engineering, product, business partners, UX research, copywriters and facility operations
Role
Sr. UX designer
Domain
Propriety enterprise apps
Consulted
Engineering, product, business partners, UX research, copywriters and facility operations
Our users

Walmart technicians are responsible for maintaining and repairing equipment in Walmart stores. Their work spans across various areas like facilities maintenance, refrigeration, HVAC (heating, ventilation, and air conditioning), and sometimes automation systems. They handle tasks like fixing broken equipment, ensuring systems like refrigerators are functioning, and performing routine maintenance to prevent issues. Technicians work across multiple locations and play a key role in keeping operations running smoothly.
Walmart technicians
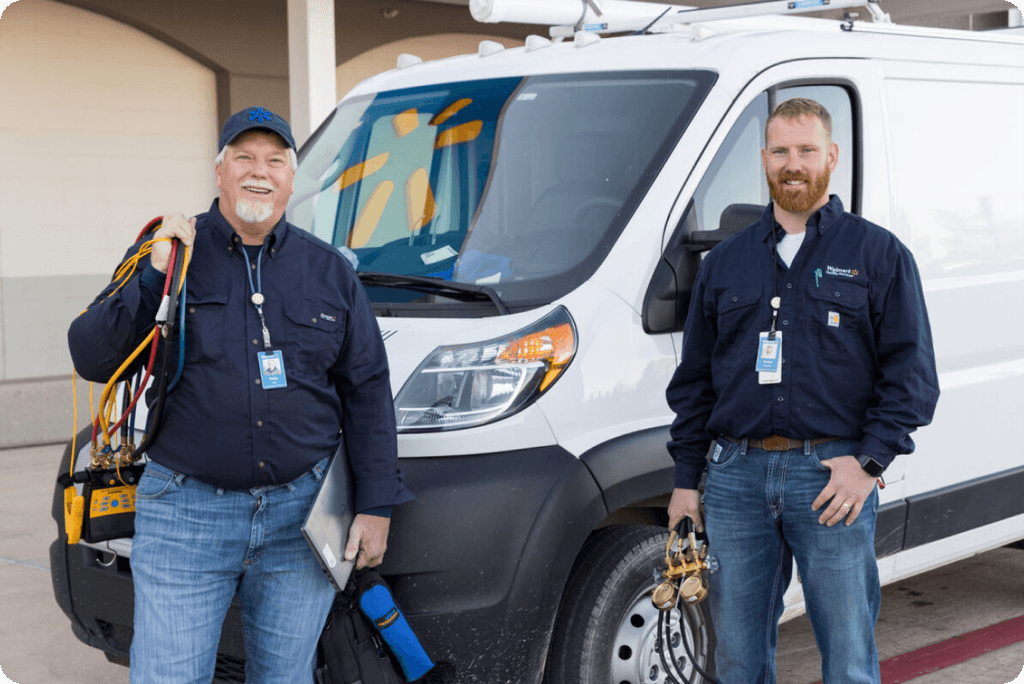
Our users

Walmart technicians
Walmart technicians are responsible for maintaining and repairing equipment in Walmart stores. Their work spans across various areas like facilities maintenance, refrigeration, HVAC (heating, ventilation, and air conditioning), and sometimes automation systems. They handle tasks like fixing broken equipment, ensuring systems like refrigerators are functioning, and performing routine maintenance to prevent issues. Technicians work across multiple locations and play a key role in keeping operations running smoothly.
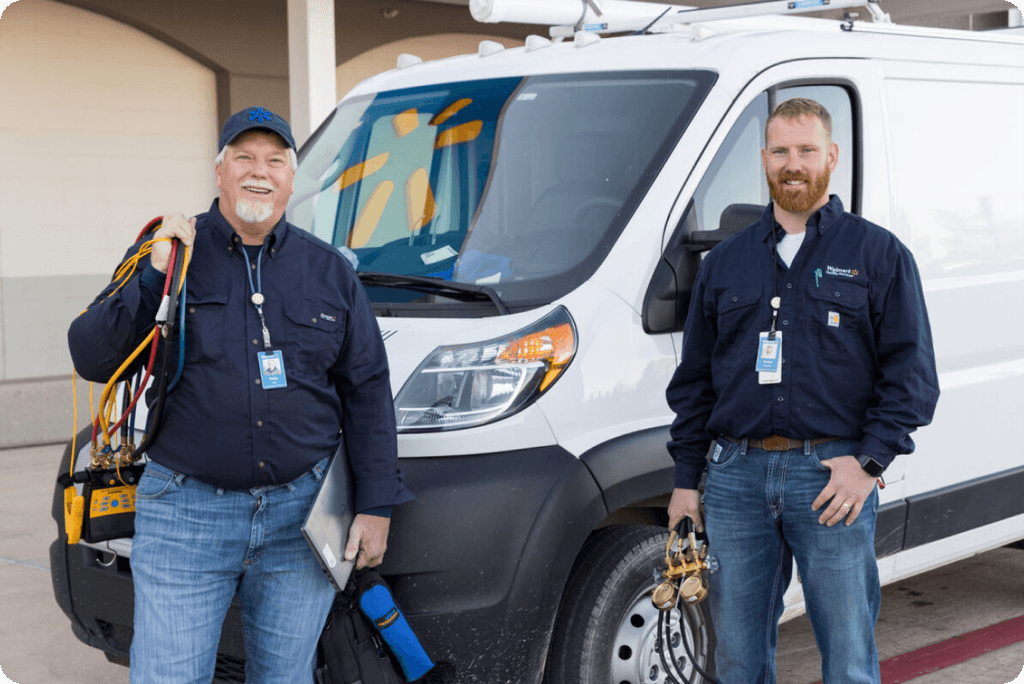
The problem

Walmart technicians currently face significant challenges with the tools they use, leading to a high turnover rate of 70%. The primary app, Field FM, suffers from latency issues, uses outdated legacy software that is difficult to update, and lacks the ability to integrate new features easily.
In addition, work orders often get lost, and technicians struggle to find relevant information, as evidenced by quotes from the field. This increases onboarding time and causes delays in managing work orders. Technicians are also required to use multiple apps—such as Zeus for ordering parts and ME@campus for tracking their time—further complicating their workflow.
The problem

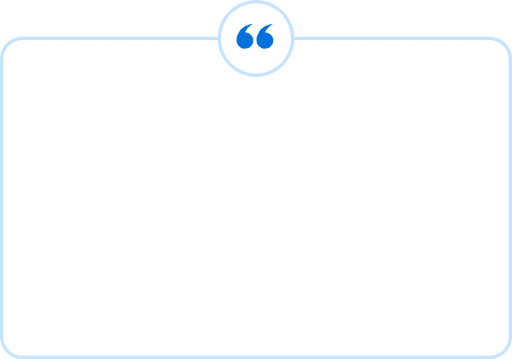
“I didn’t know what I was looking at. It takes a good month to get use to this (Field FM app).”
-Ron, GM Technician
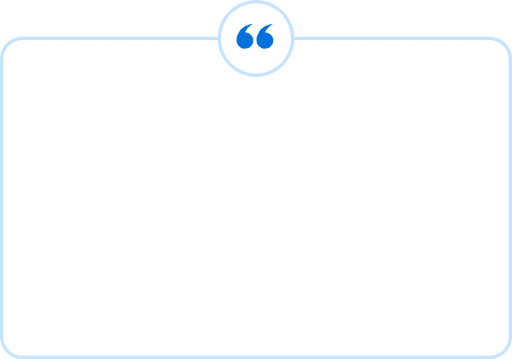
“I didn’t know what I was looking at. It takes a good month to get use to this (Field FM app).”
-Ron, GM Technician
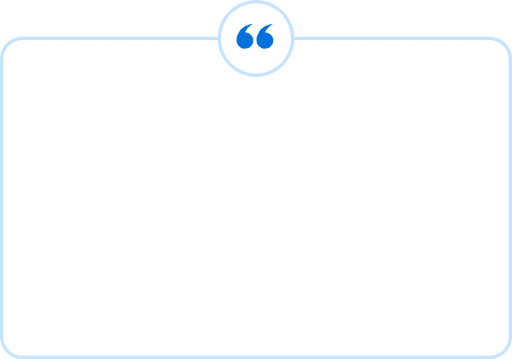
“I didn’t know what I was looking at. It takes a good month to get use to this (Field FM app).”
-Ron, GM Technician
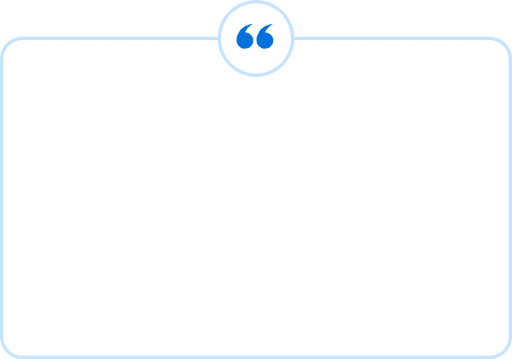
“I get worried about aging work orders. Sometimes they get lost and you don’t have them available.”
-Kett, Refrigeration Technician
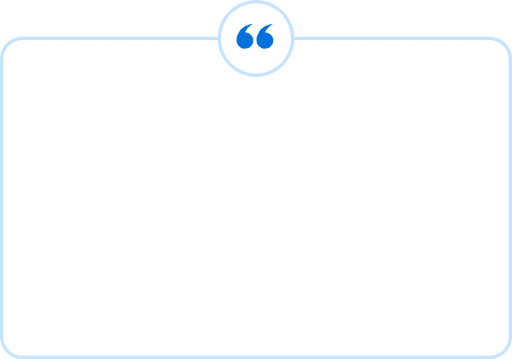
“I get worried about aging work orders. Sometimes they get lost and you don’t have them available.”
-Kett, Refrigeration Technician
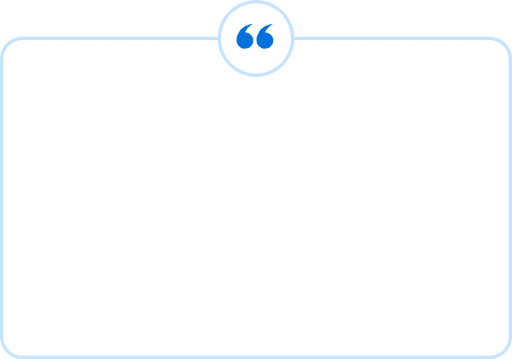
“I get worried about aging work orders. Sometimes they get lost and you don’t have them available.”
-Kett, Refrigeration Technician
The process
The process

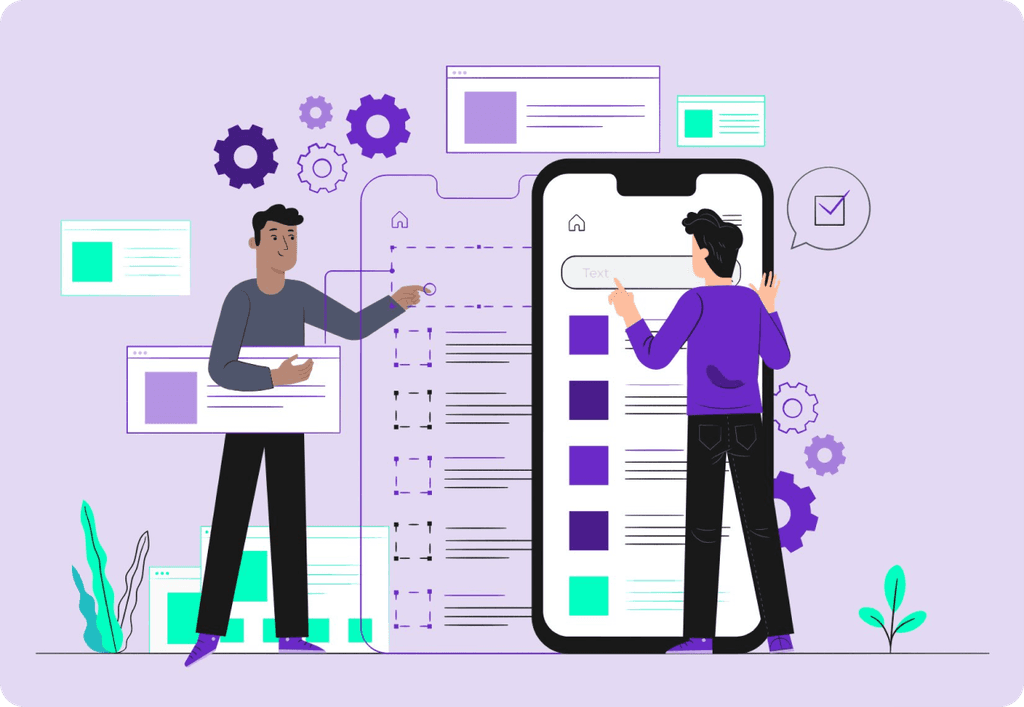
Discovery
Understanding users
User feedback on legacy app
Opportunity
User journey map
Design
Site map
User research
Qualitative - moderated user testing
Final design
Prototype
Engineering hand off
Accessibility annotations
What's next
How are we measuring success?
Enhancements
Discovery
Understanding users
User feedback on legacy app
Opportunity
User journey map
Design
Site map
User research
Qualitative - moderated user testing
Final design
Prototype
Engineering hand off
Accessibility annotations
What's next
How are we measuring success?
Enhancements
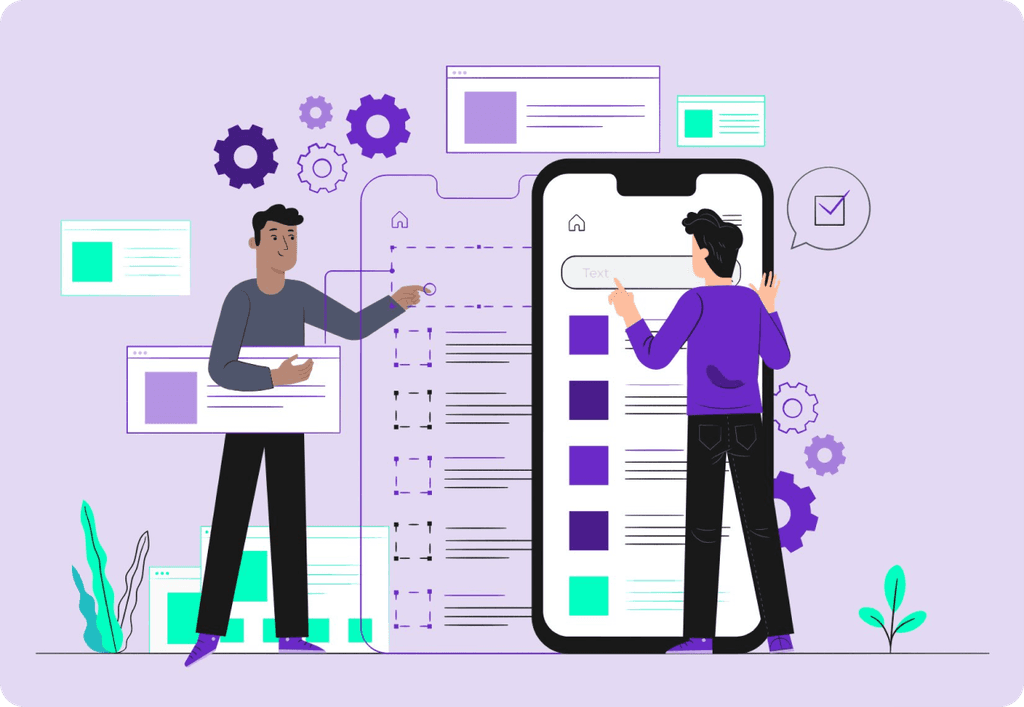
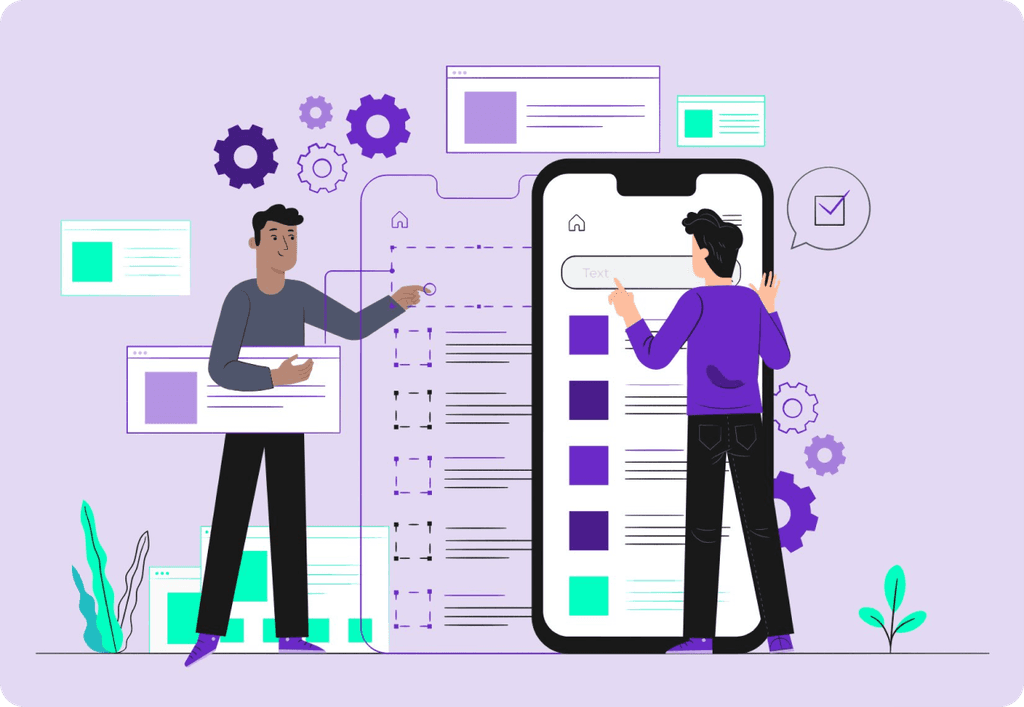
The process

Opportunity

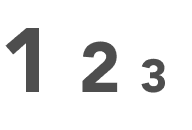
Improve Information
hierarchy
Improving the organization of details within each work order to minimize onboarding time, help technicians get aligned faster, and prevent orders from being overlooked.
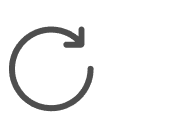
Reduce turnover
Provide a more intuitive, efficient tool that reduces frustration and errors, ultimately improving job satisfaction and lowering the 70% technician turnover rate.
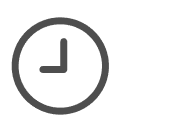
Increase efficiency
Improving the organization of details within each work order to minimize onboarding time, help technicians get aligned faster, and prevent orders from being overlooked.
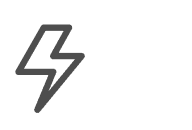
Optimize
performance
Optimize performance
Address latency issues by migrating from legacy software to a modern, easily upgradable system, ensuring faster response times and the ability to implement new features without delay.
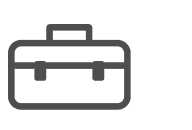
Consolidate tools
Combine multiple tools (Field FM, Zeus, navigation, timeclock) into a single app to streamline workflows and reduce the complexity of managing tasks across different platforms.
Opportunity

User journey
User journey

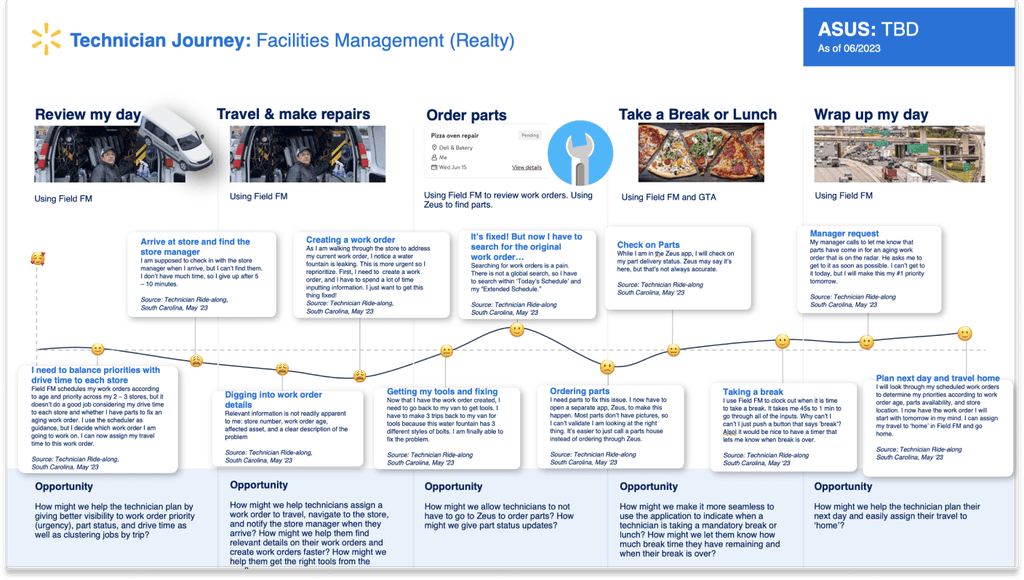
Understanding the Technician Experience
We conducted technician interviews to capture their pain points and positive experiences throughout their day. These insights allowed us to create a journey map that served as a valuable tool for feature ideation, facilitating discussions with the business, and building empathy for the challenges technicians face.
Understanding the Technician Experience
We conducted technician interviews to capture their pain points and positive experiences throughout their day. These insights allowed us to create a journey map that served as a valuable tool for feature ideation, facilitating discussions with the business, and building empathy for the challenges technicians face.
User Journey

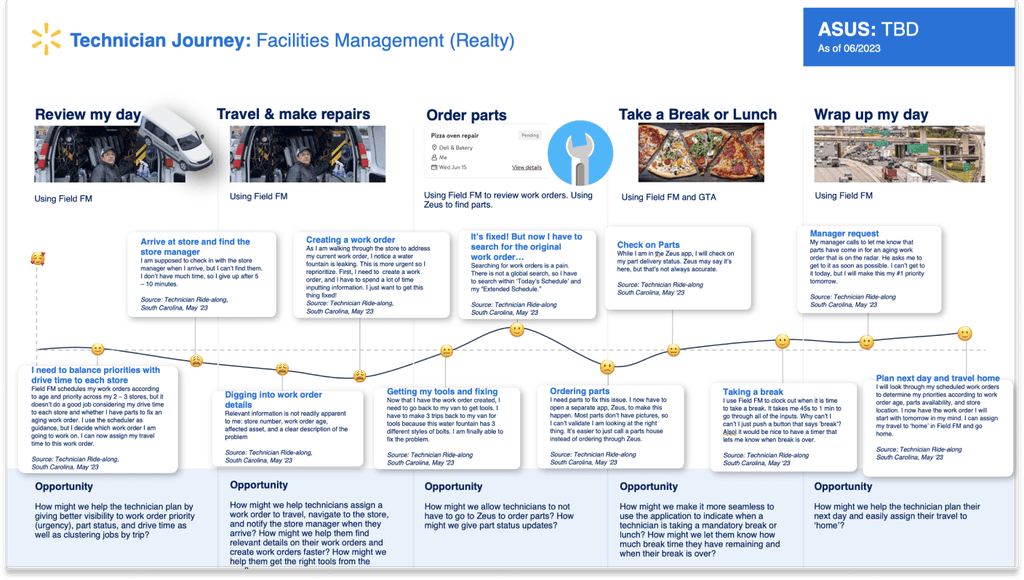
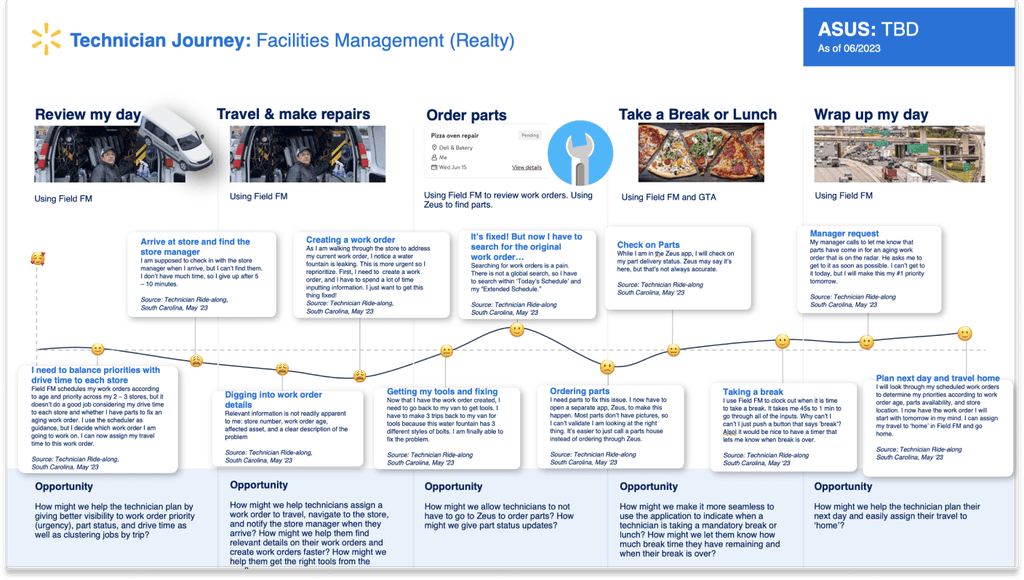
Information architecture
Creating a site map was crucial in establishing a clear structure for the new app. It helped us visualize the overall flow, define content organization, and identify key interactions for technicians. By mapping out the app's architecture, we ensured a logical and intuitive navigation system, which reduced complexity and minimized the learning curve for users. The site map also served as a valuable communication tool, aligning stakeholders on the app’s structure and guiding feature prioritization throughout the design process.
Site map

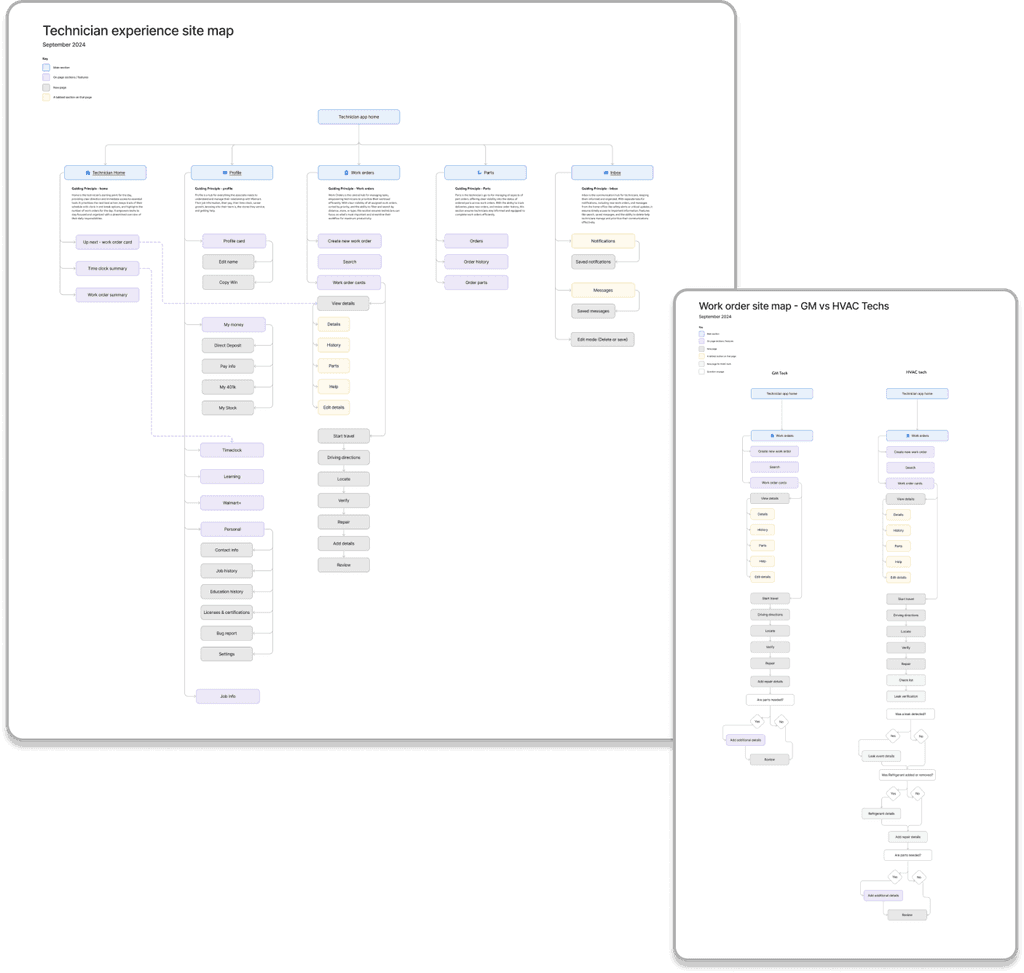
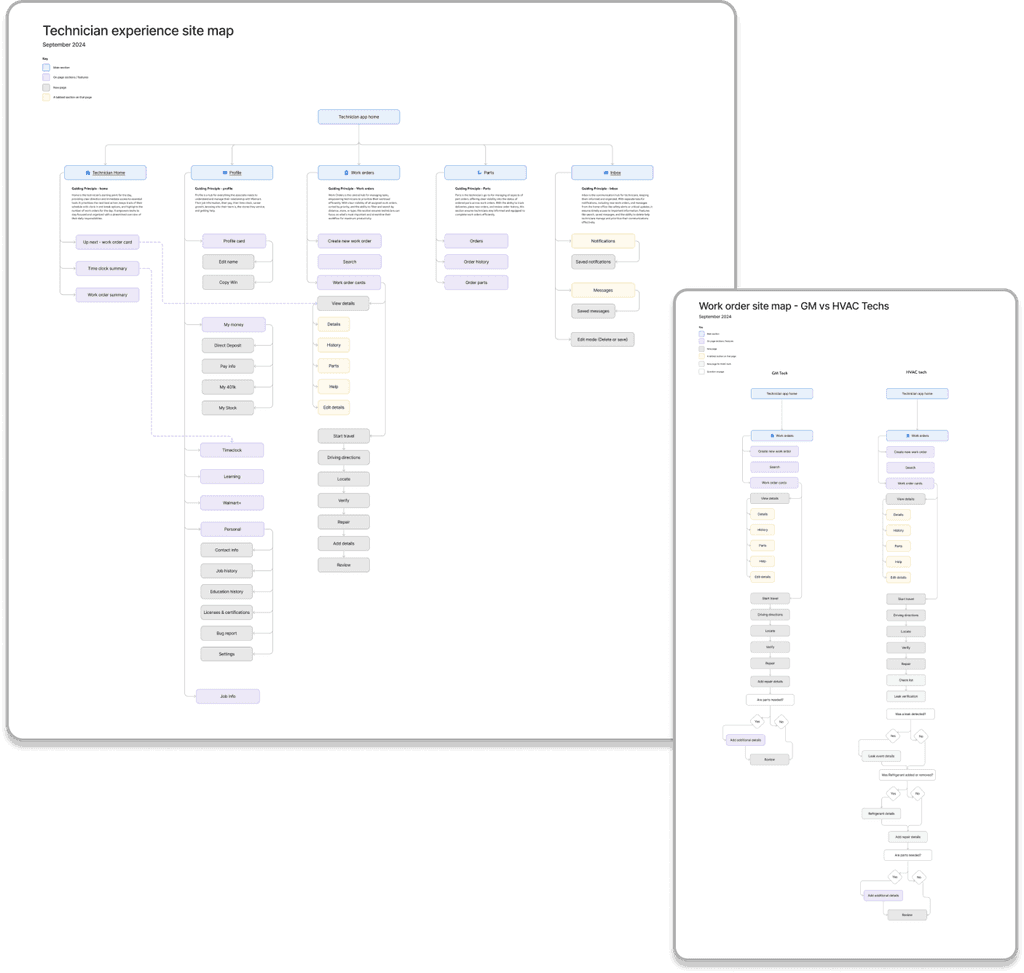
Site map
Site map

Information architecture
Creating a site map was crucial in establishing a clear structure for the new app. It helped us visualize the overall flow, define content organization, and identify key interactions for technicians. By mapping out the app's architecture, we ensured a logical and intuitive navigation system, which reduced complexity and minimized the learning curve for users. The site map also served as a valuable communication tool, aligning stakeholders on the app’s structure and guiding feature prioritization throughout the design process.
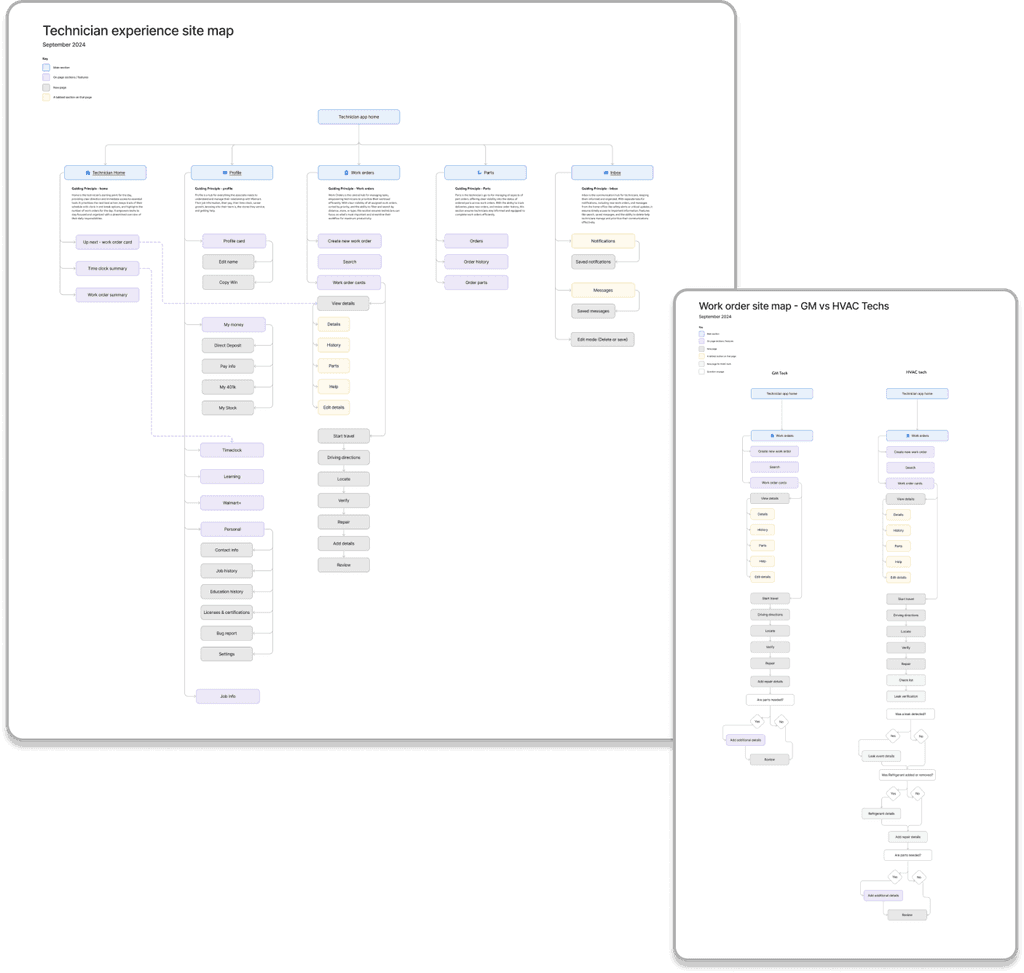
Gen Ai
Gen Ai

Problem area: High cost of outsourcing
Walmart incurs a high cost of outsourcing when technicians are routed inefficiently, or when they focus on the wrong thing.
Solution
We are incorporating machine learning and generative AI. This way we can automate the sorting of work orders for technicians so that we always lead them to their next best action. The system will consider the priority, technicians current location and time it takes to complete each work order.
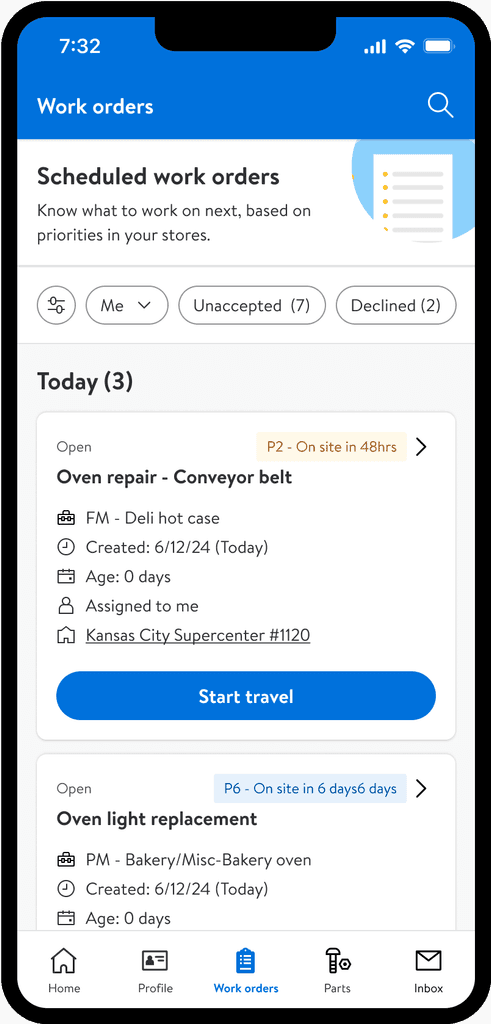
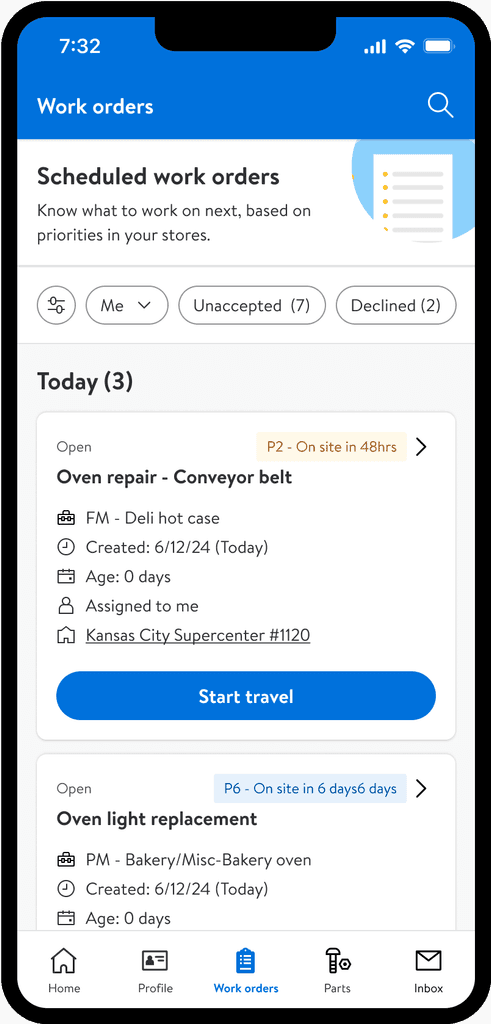
User research
User research

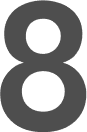
Moderated user tests
Moderated user tests
It was crucial for us to get the repair flow correct since it’s the most frequent task technicians perform, and any confusion or inefficiency could significantly impact their productivity and overall experience.
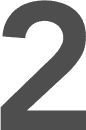
Distinct perspectives
Distinct perspectives
6 Experienced technicians
2 New to the job - less experienced technicians
6 Experienced technicians
2 New to the job - less experienced technicians.
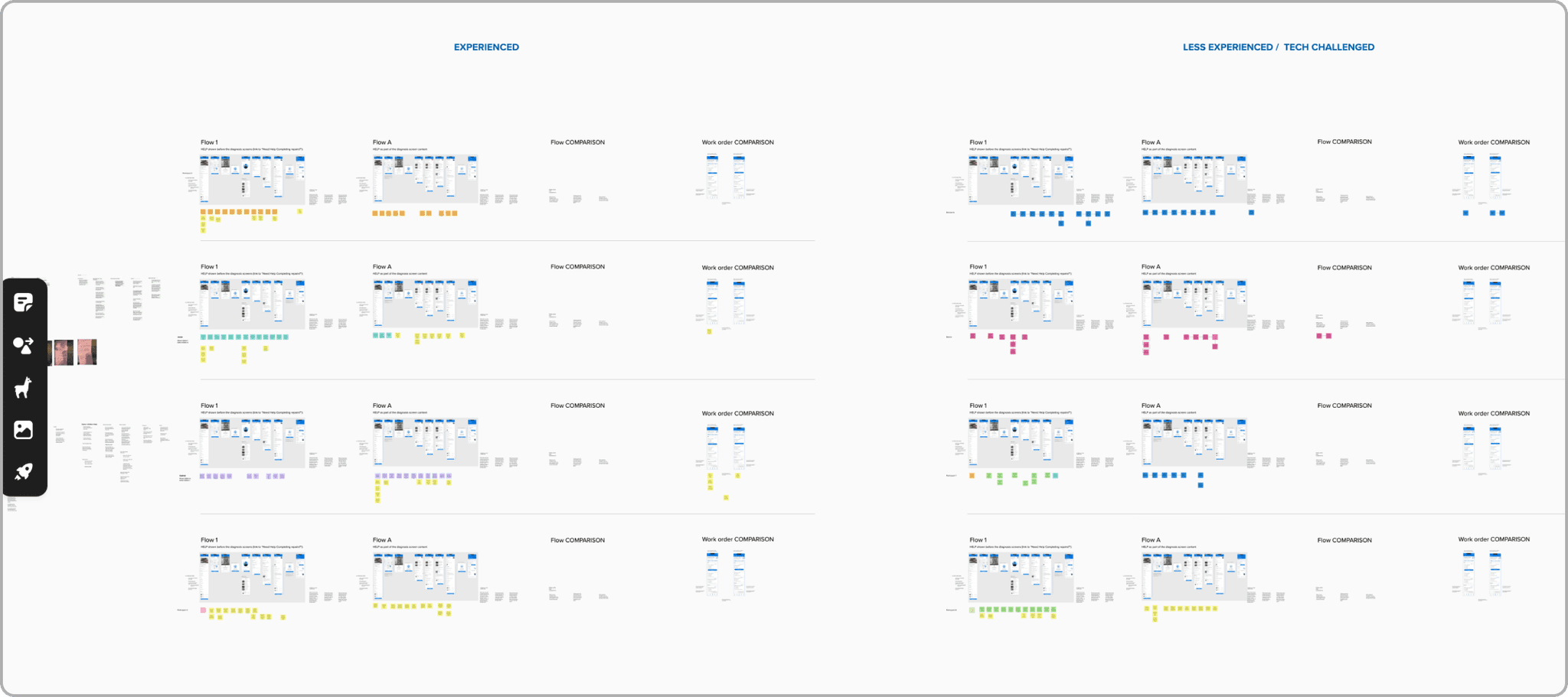
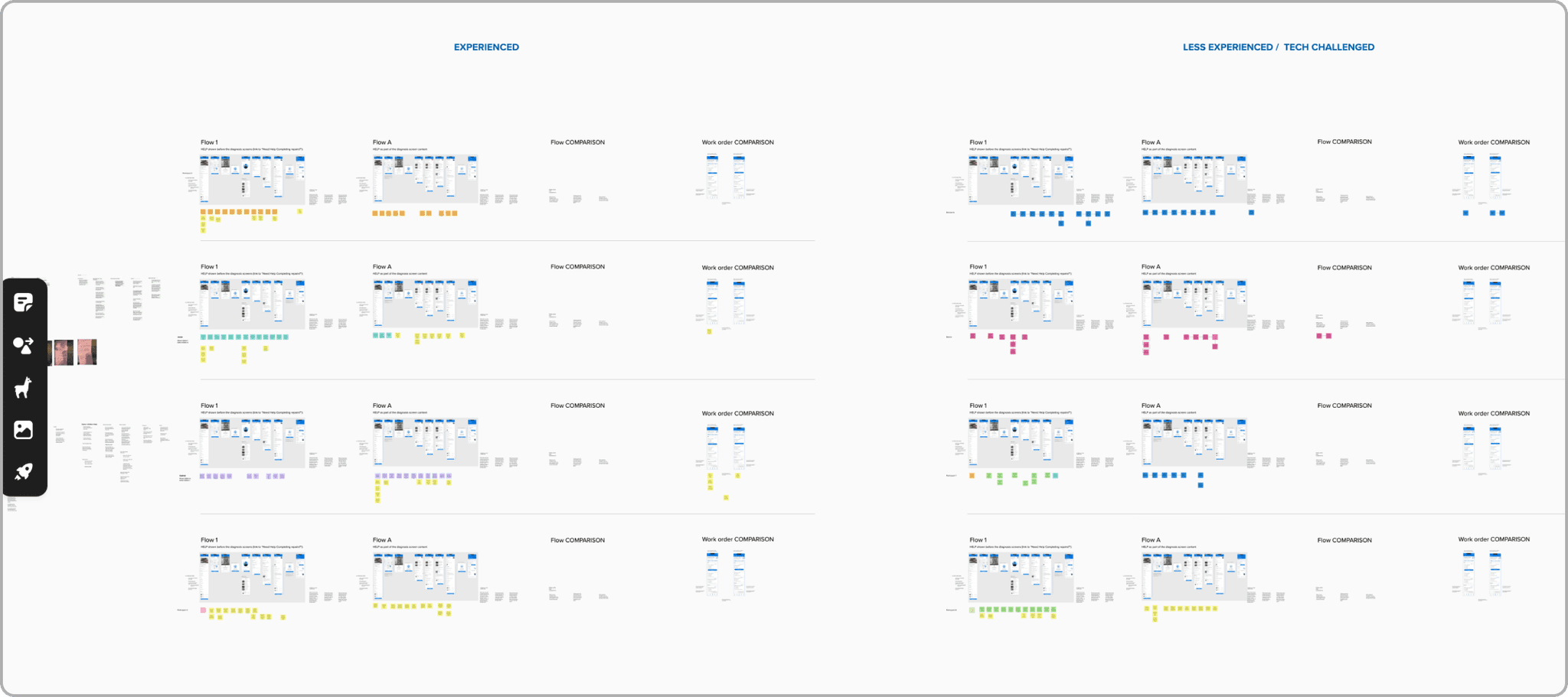
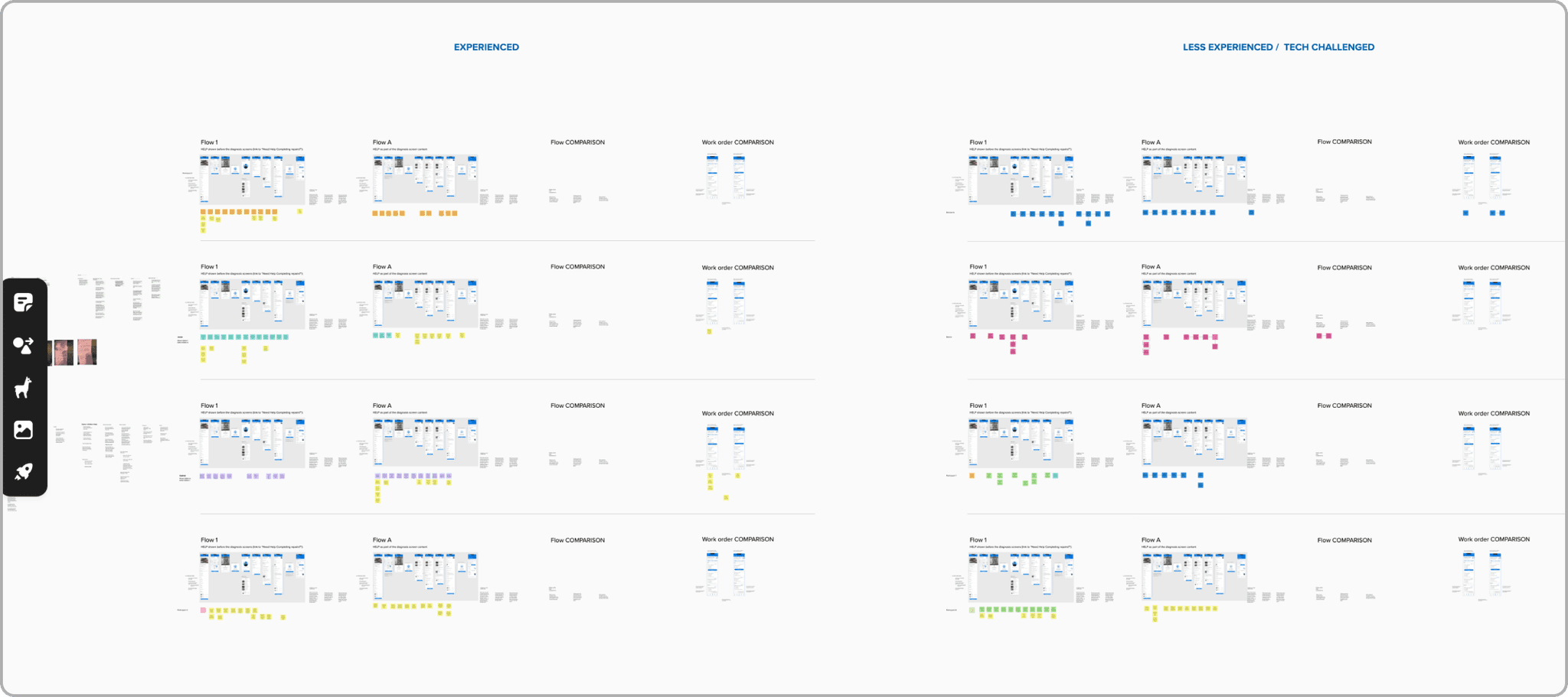
User research

Insights & findings

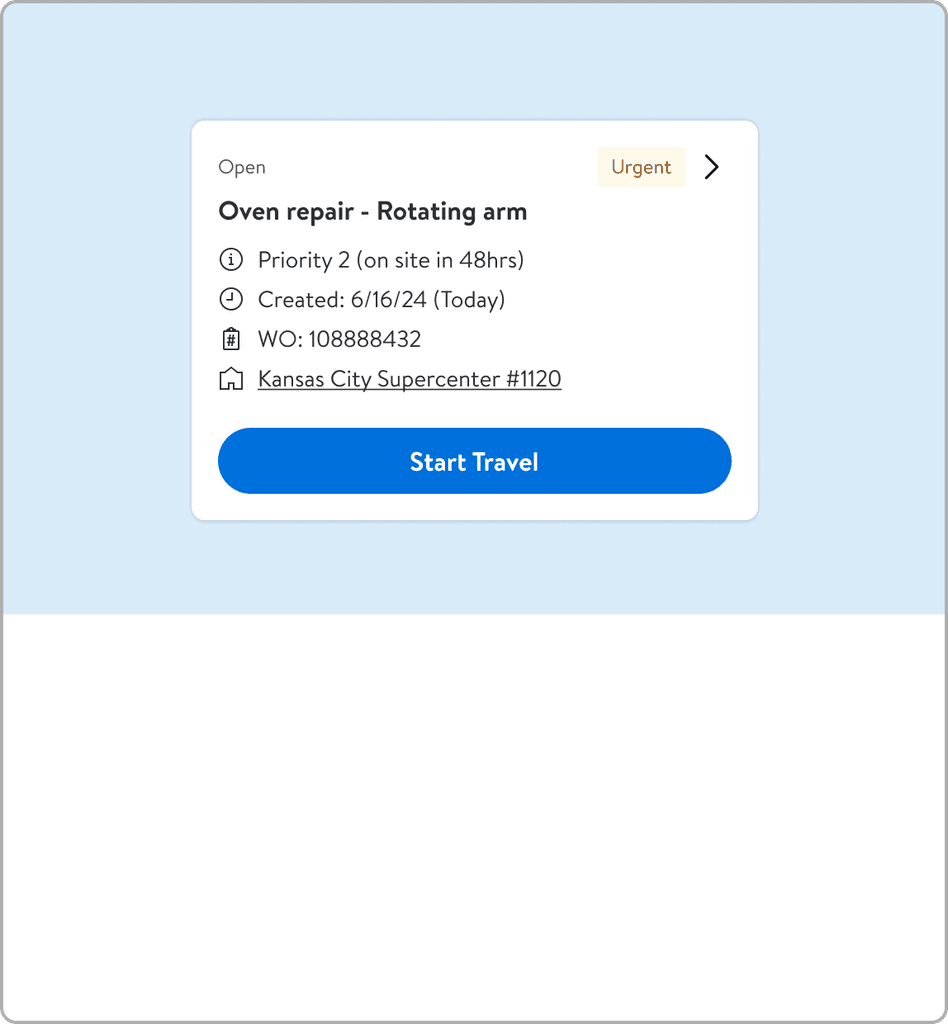
Streamline the details
Streamline the details
Focus on the key information by showing only the top 4 data points on work order cards. Technicians prioritize knowing the type of repair and its location, preferring to dive into the finer details once they’re on-site.
Focus on the key information by showing only the top 4 data points on work order cards. Technicians prioritize knowing the type of repair and its location, preferring to dive into the finer details once they’re on-site.
Streamline the details
Focus on the key information by showing only the top 4 data points on work order cards. Technicians prioritize knowing the type of repair and its location, preferring to dive into the finer details once they’re on-site.
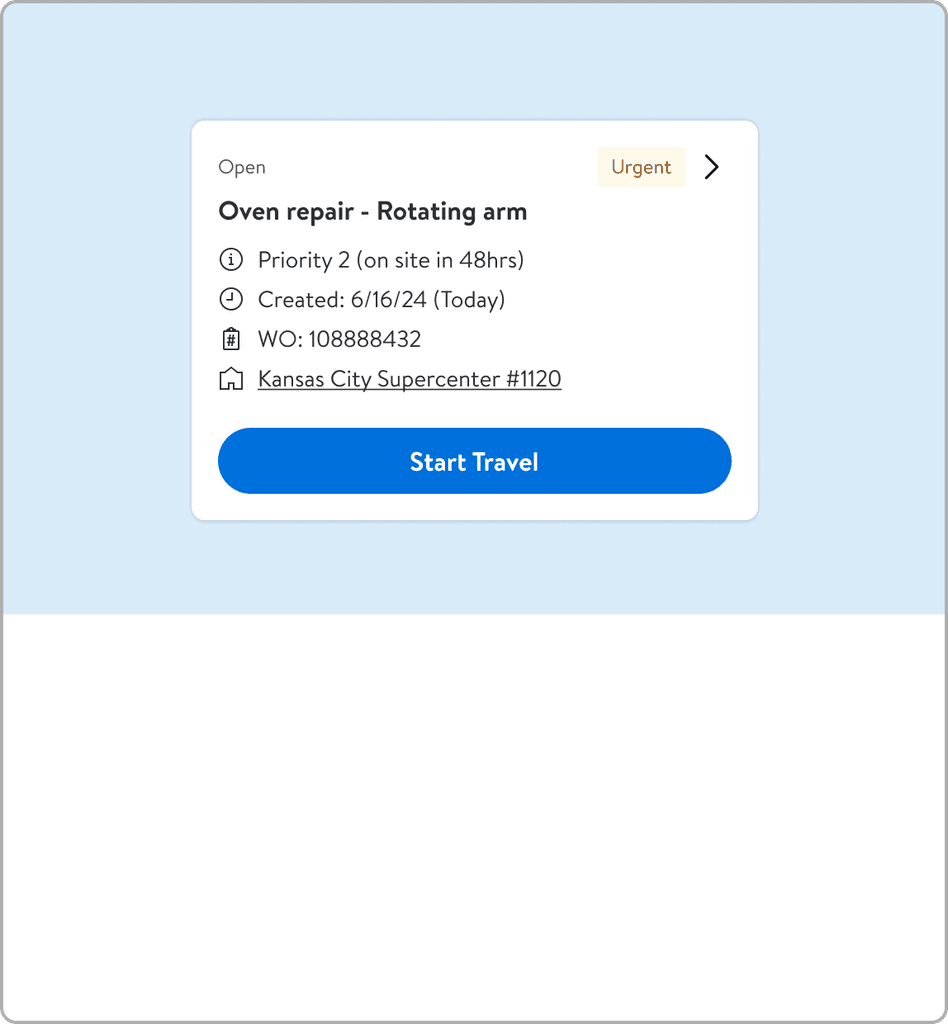
Streamline the details
Focus on the key information by showing only the top 4 data points on work order cards. Technicians prioritize knowing the type of repair and its location, preferring to dive into the finer details once they’re on-site.
Streamline the details
Focus on the key information by showing only the top 4 data points on work order cards. Technicians prioritize knowing the type of repair and its location, preferring to dive into the finer details once they’re on-site.
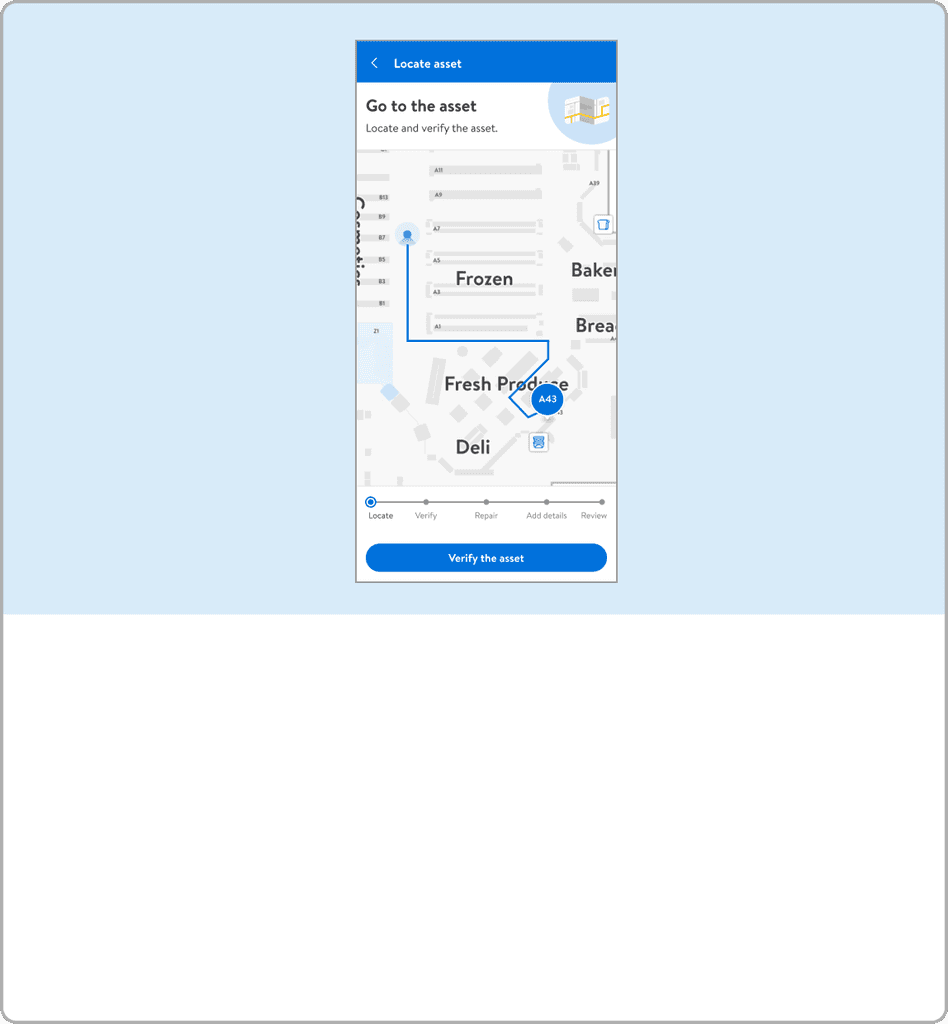
Reduce time locating assets
Reduce time locating assets
Technicians frequently lose valuable time searching for the asset needing repair when they arrive at a store. User testing indicated a strong preference for a map feature, so we incorporated the “item location” functionality from our associate experience team into the MVP.
Technicians frequently lose valuable time searching for the asset needing repair when they arrive at a store. User testing indicated a strong preference for a map feature, so we incorporated the “item location” functionality from our associate experience team into the MVP.
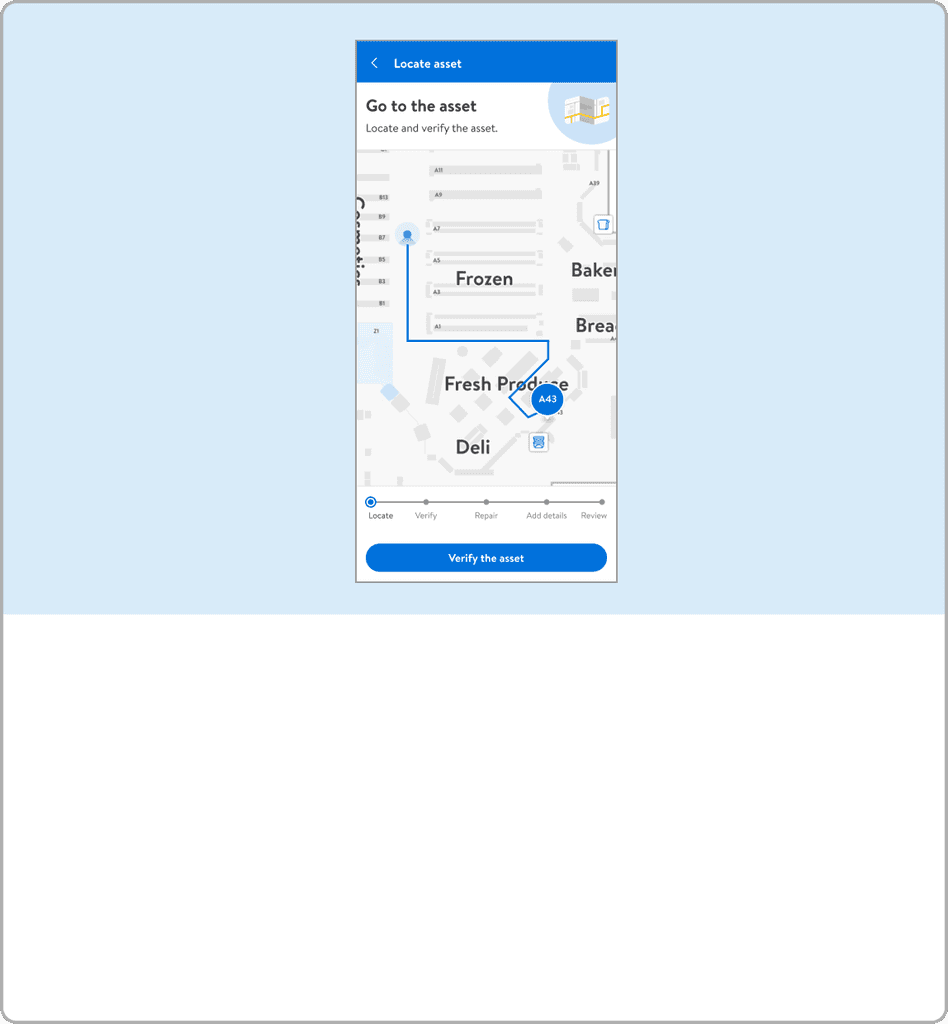
Reduce time locating assets
Technicians frequently lose valuable time searching for the asset needing repair when they arrive at a store. User testing indicated a strong preference for a map feature, so we incorporated the “item location” functionality from our associate experience team into the MVP.
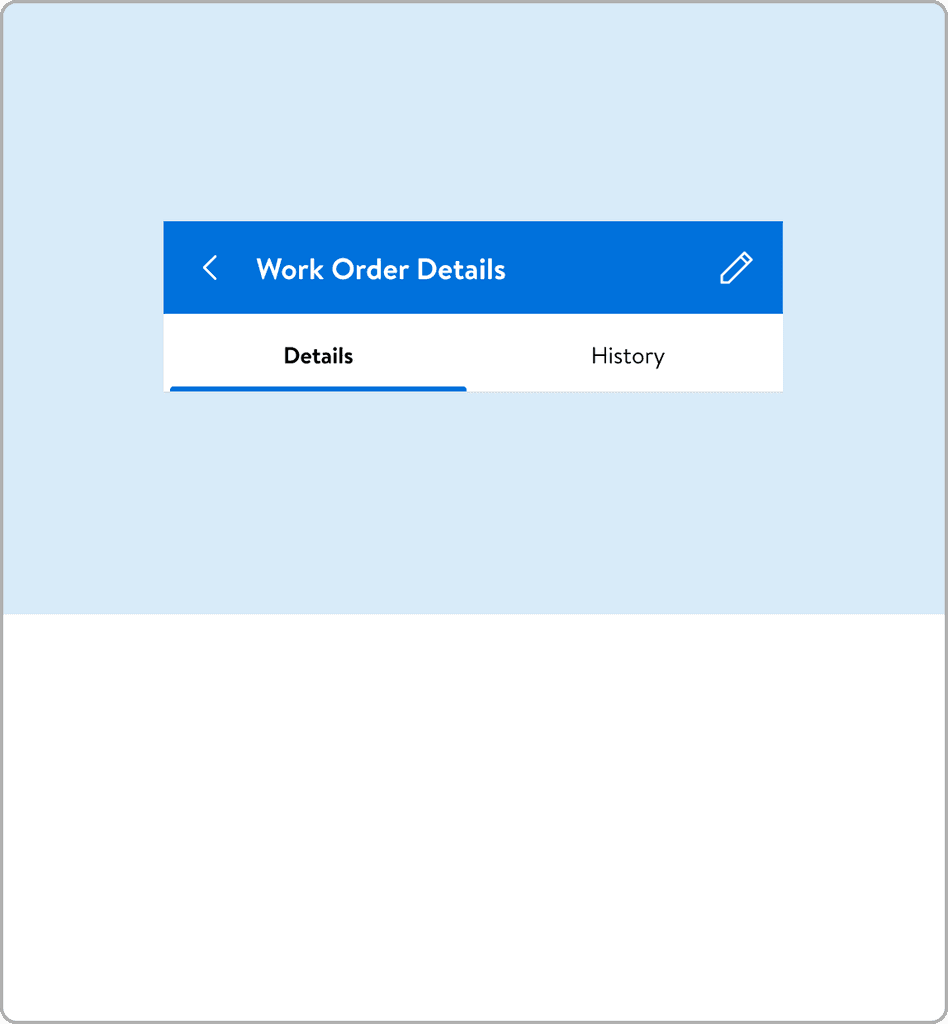
Include a history section
Include a history section
Technicians wanted visibility into the work order’s history—seeing if it was started by another technician, reassigned, or if parts had been ordered—all critical details to understand the status and context of the task.
Technicians wanted visibility into the work order’s history—seeing if it was started by another technician, reassigned, or if parts had been ordered—all critical details to understand the status and context of the task.
Include a history section
Technicians wanted visibility into the work order’s history—seeing if it was started by another technician, reassigned, or if parts had been ordered—all critical details to understand the status and context of the task.
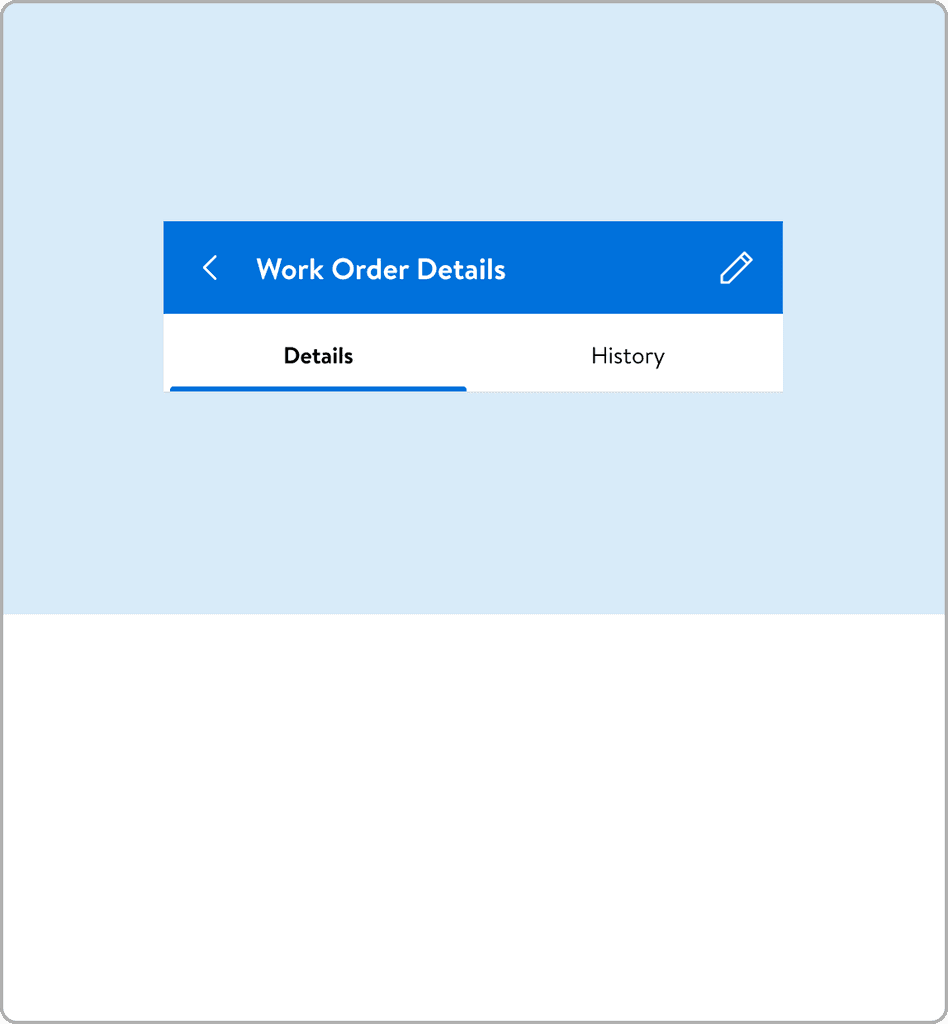
Include a history section
Technicians wanted visibility into the work order’s history—seeing if it was started by another technician, reassigned, or if parts had been ordered—all critical details to understand the status and context of the task.
Include a history section
Technicians wanted visibility into the work order’s history—seeing if it was started by another technician, reassigned, or if parts had been ordered—all critical details to understand the status and context of the task.
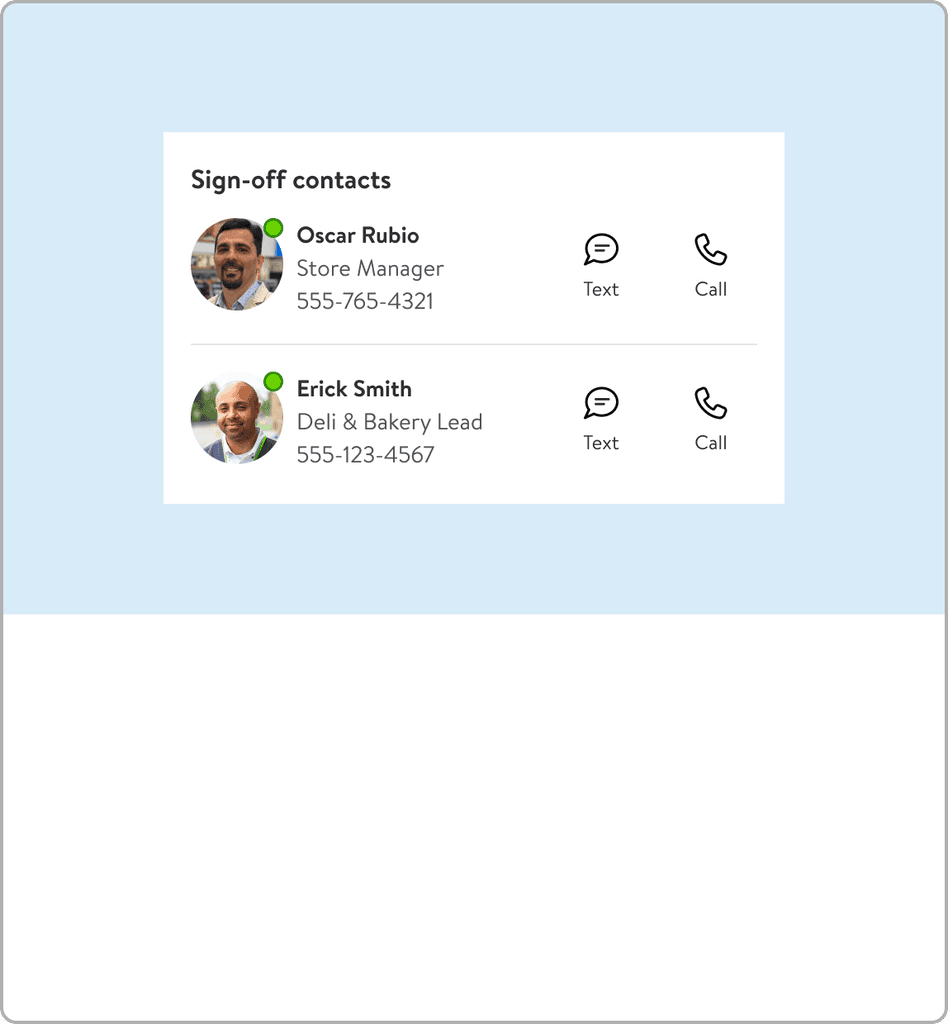
Quick Access to Sign-Off Contacts
Quick Access to Sign-Off Contacts
Technicians need more than just a name for sign-off; they wanted a quick and easy way to reach their contact, whether through a text or a call. Including a photo of the contact also helps technicians identify the right person when arriving at the store.
Technicians need more than just a name for sign-off; they wanted a quick and easy way to reach their contact, whether through a text or a call. Including a photo of the contact also helps technicians identify the right person when arriving at the store.
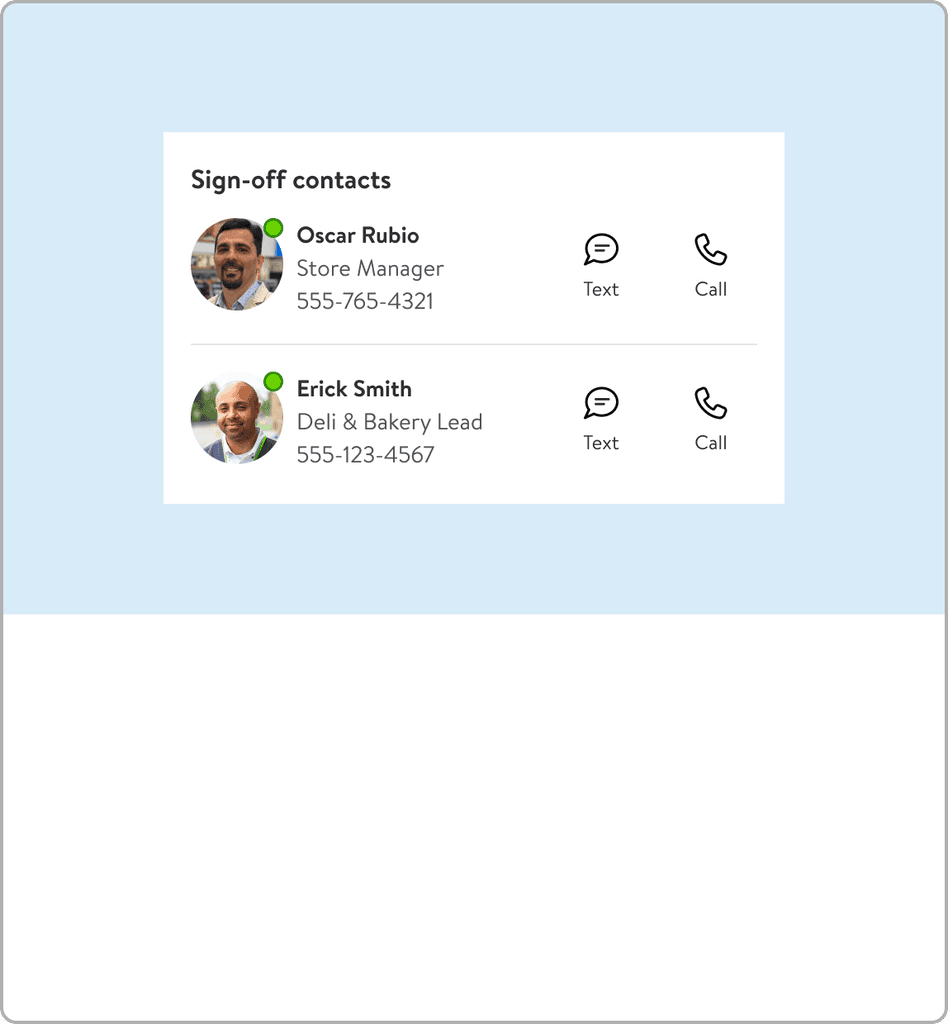
Quick Access to Sign-Off Contacts
Technicians need more than just a name for sign-off; they wanted a quick and easy way to reach their contact, whether through a text or a call. Including a photo of the contact also helps technicians identify the right person when arriving at the store.
Insights & findings

MVP
MVP

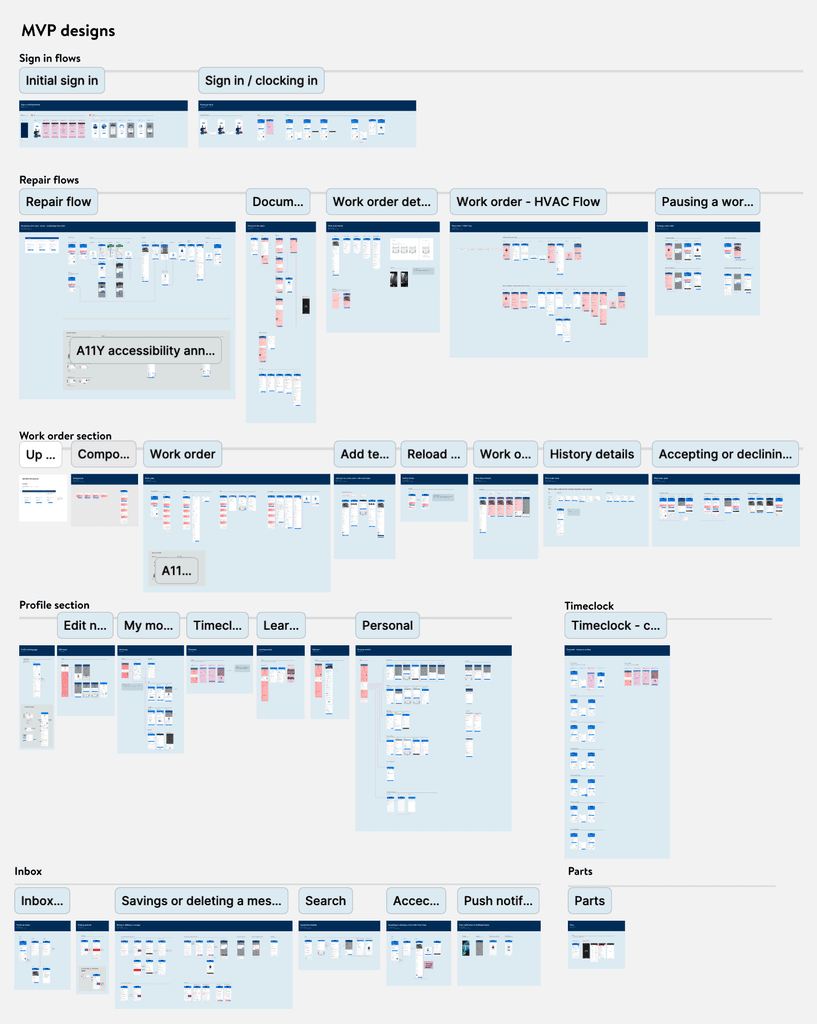
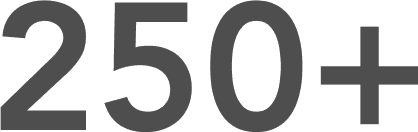
Key screens
We designed over 250 key screens as part of the Minimum Viable Product (MVP) to ensure that every aspect of the technician workflow was thoughtfully addressed. From task prioritization and work order management to parts ordering and reporting, the extensive design work laid the foundation for a robust and comprehensive app experience.
Key screens
We designed over 250 key screens as part of the Minimum Viable Product (MVP) to ensure that every aspect of the technician workflow was thoughtfully addressed. From task prioritization and work order management to parts ordering and reporting, the extensive design work laid the foundation for a robust and comprehensive app experience.
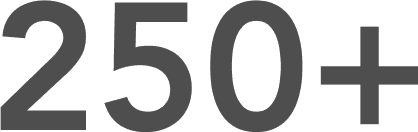
MVP

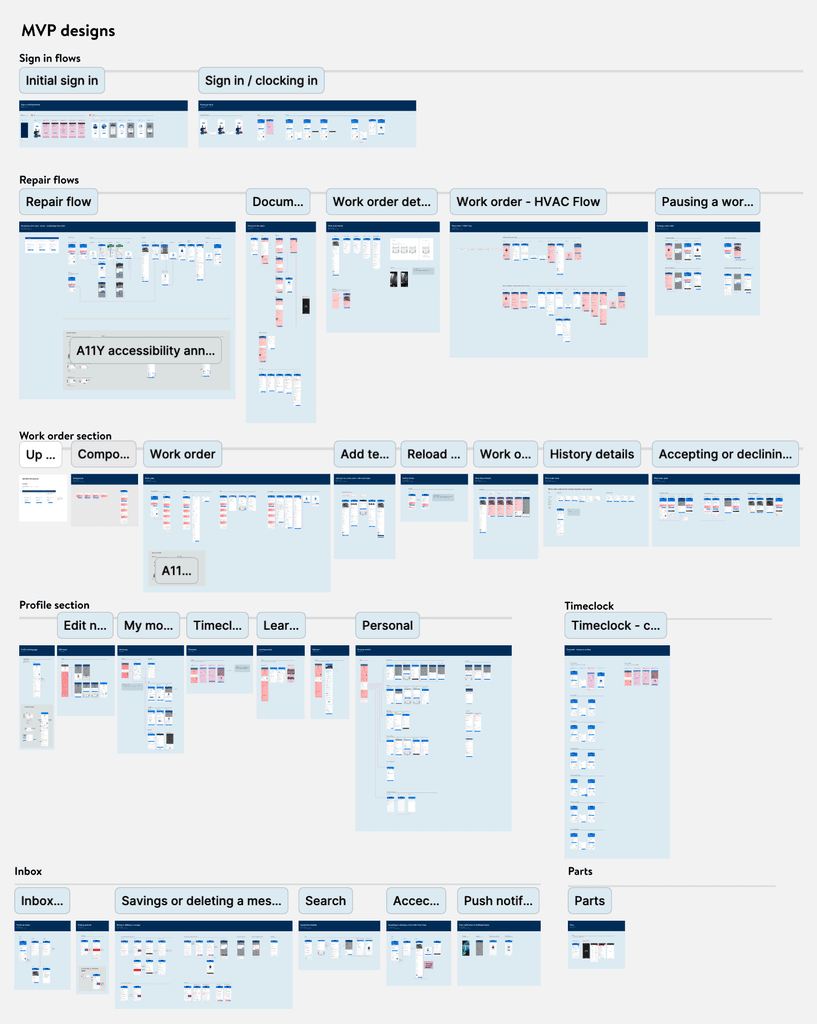
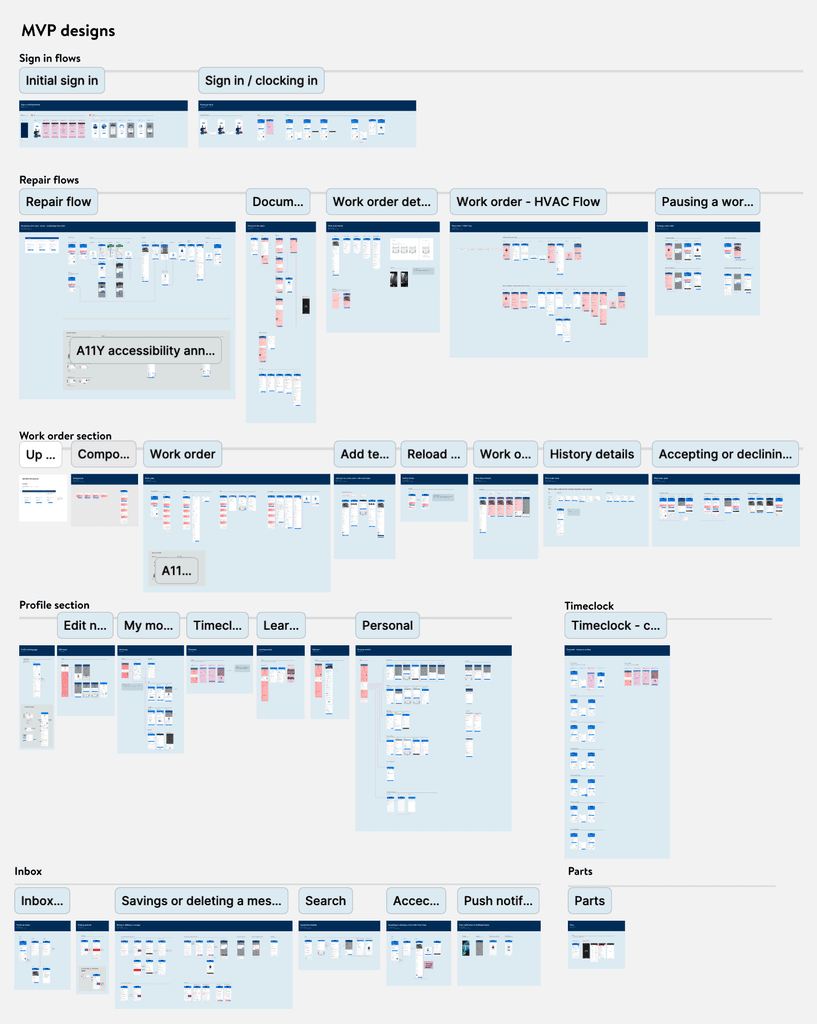
Final Designs

Final Designs

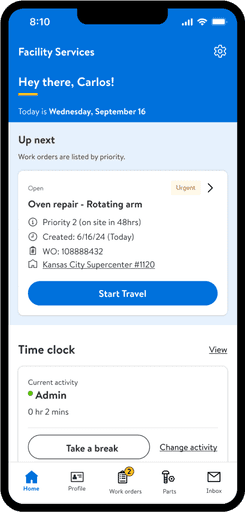
A technician is guided to their next best action, but can also easily see work orders for the day, week etc.
A technician is guided to their next best action, but can also easily see work orders for the day, week etc.
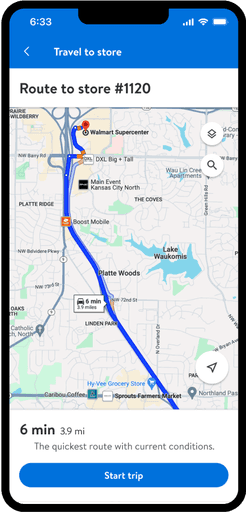
The technician can opt for a guided route via Google maps integrated into the app.
The technician can opt for a guided route via Google maps integrated into the app.
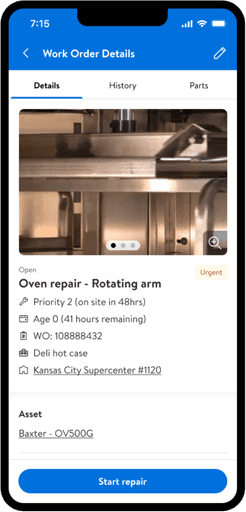
The Once they arrive at the store, the technician can view the work order details, before we guide them with in store maps to the asset.
The Once they arrive at the store, the technician can view the work order details, before we guide them with in store maps to the asset.
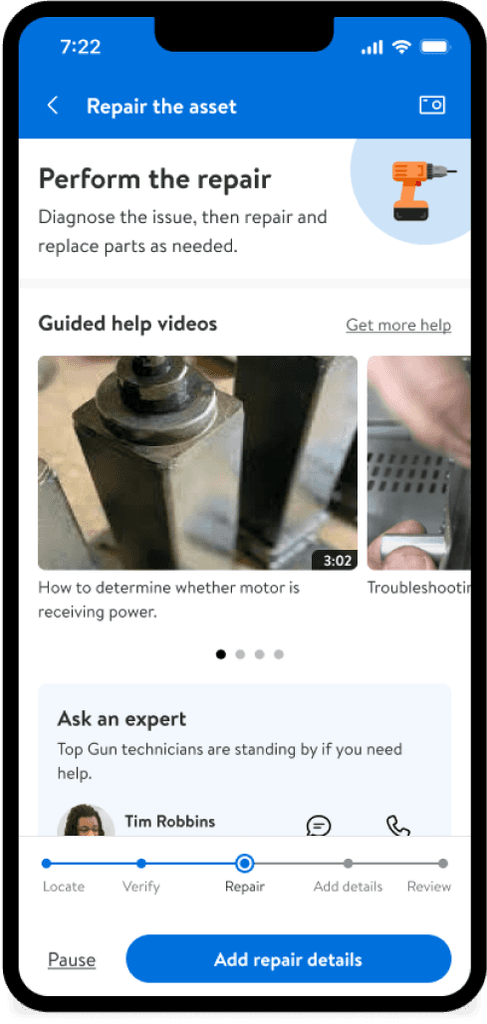
The technician also has relevant asset help content specific to the repair at their fingertips.
The technician also has relevant asset help content specific to the repair at their fingertips.
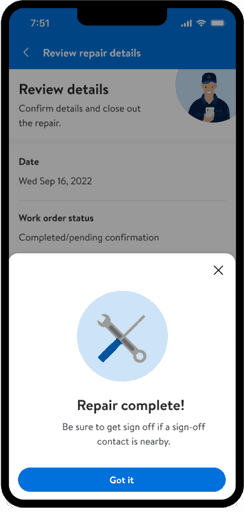
Once the repair is completed they review the details they added and move to their next task
Once the repair is completed they review the details they added and move to their next task
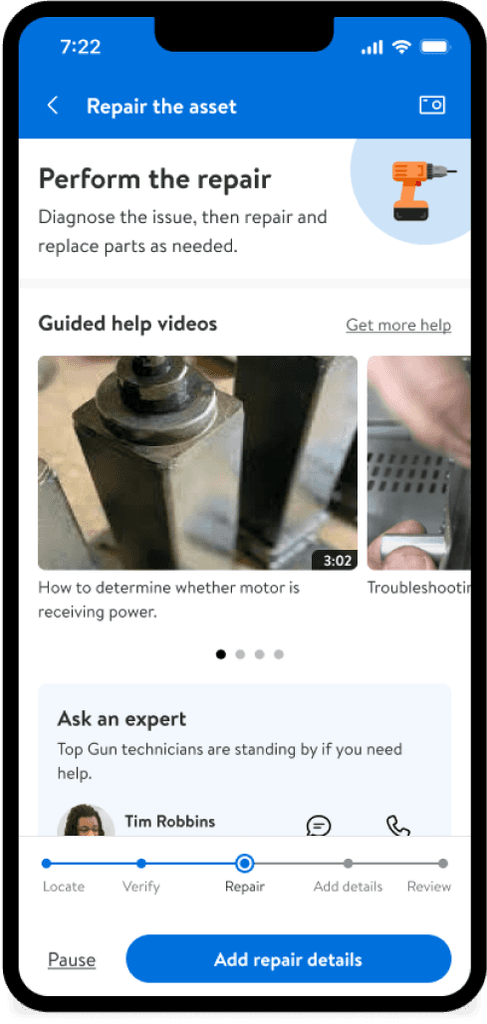
The technician also has relevant asset help content specific to the repair at their fingertips.
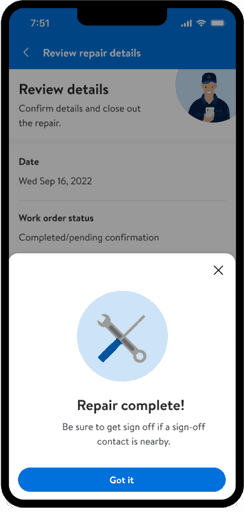
Once the repair is completed they review the details they added and move to their next task
How are we measuring success?
How are we measuring success?

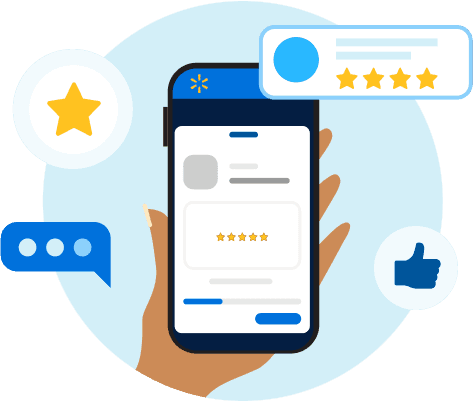
Reducing windshield time & turnover
Reducing windshield time & turnover
The main KPIs for this app are reducing windshield time—measuring how efficiently technicians respond to and complete work orders—and a decrease in technician turnover, which currently sits at 70%.
The main KPIs for this app are reducing windshield time—measuring how efficiently technicians respond to and complete work orders—and a decrease in technician turnover, which currently sits at 70%.
Reducing windshield time & turnover
The main KPIs for this app are reducing windshield time—measuring how efficiently technicians respond to and complete work orders—and a decrease in technician turnover, which currently sits at 70%.
How are we measuring success?

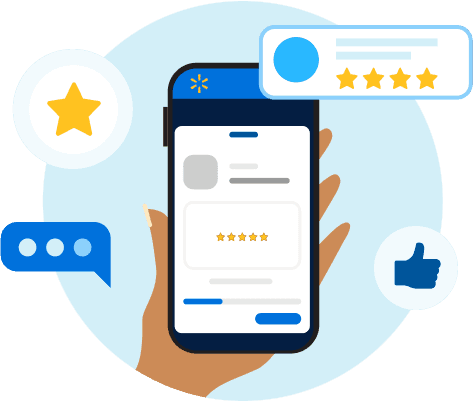
What's next?
What's next?

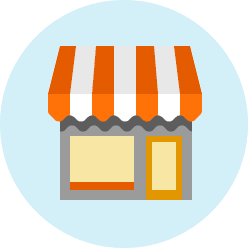
Expanding to chain
The new app will be piloted in 60 regions and plans to expand to all by late 2025.
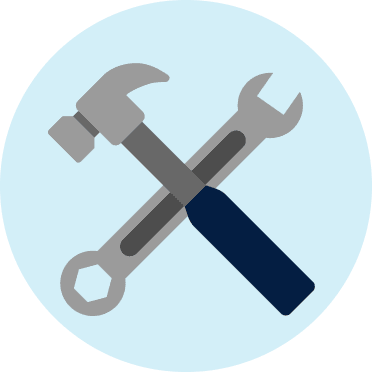
Add more functionality
We plan to add additional help content for performing repairs, increase personalization, and include parts ordering within the app—a feature that had to be cut due to timeline constraints and engineering resources.
What's next?

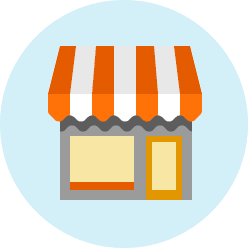
Expanding to chain
The new app will be piloted in 60 regions and plans to expand to all by late 2025.
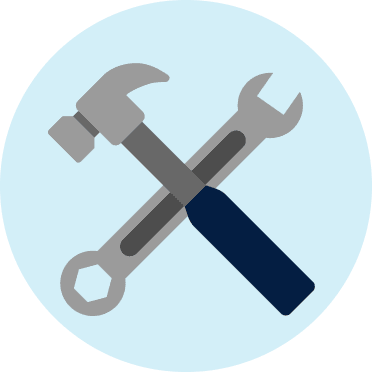
Add more functionality
We plan to add additional help content for performing repairs, increase personalization, and include parts ordering within the app—a feature that had to be cut due to timeline constraints and engineering resources.
Gen Ai

Problem area: High cost of outsourcing
Walmart incurs a high cost of outsourcing when Technicians are routed inefficiently, or when they focus on the wrong thing.
Solution
We are incorporating machine learning and generative AI. This way we can automate the sorting of work orders for technicians so that we always lead them to their next best action. The system will consider the priority, technicians current location and time it takes to complete each work order.
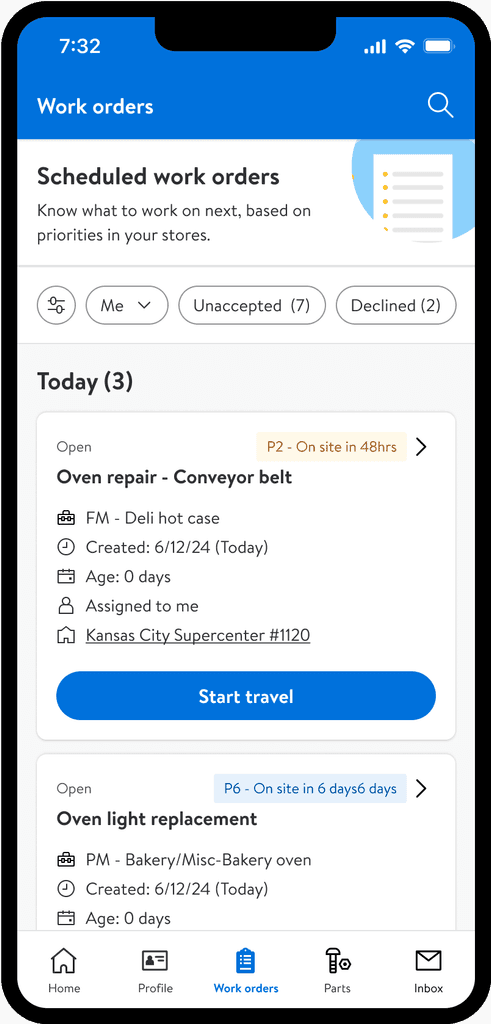
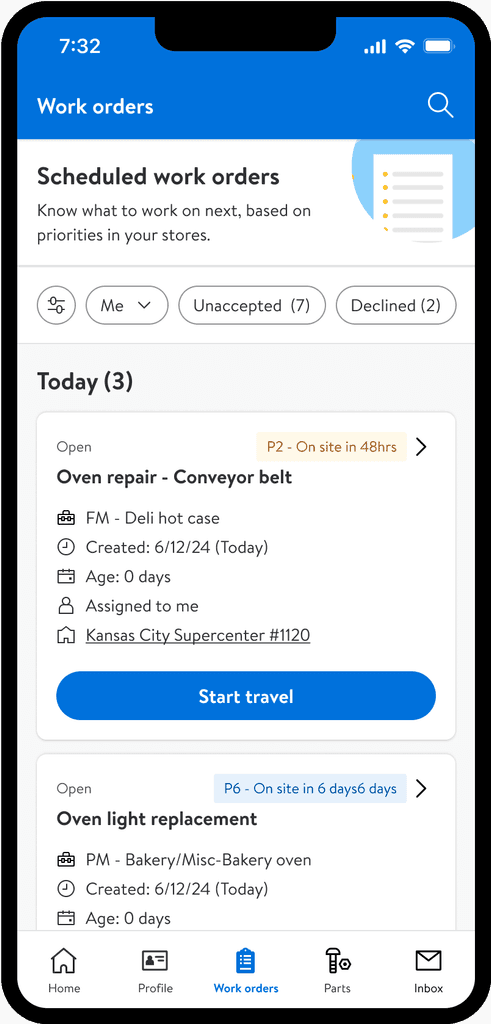